in a recent article on electronic products and technology, sat sandhu of fluke corporation outlined how thermal imaging (ti) cameras can be used by engineers to map out heat patterns and discover hotspots on electronic devices and components, an important step in thermal management.
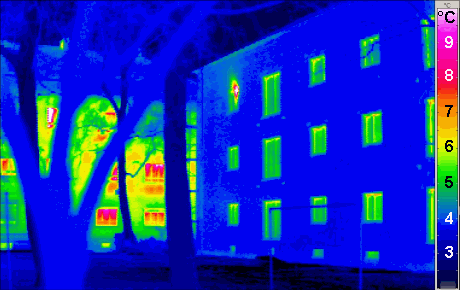
thermography can be used in testing electronics. (wikimedia commons)
sandhu noted that ti cameras can measure temperature while avoiding contact with the component and potentially affecting the data and can also give a picture of the whole system rather than just a single point.
the article goes further into the importance of thermal management for electronics. improving heat dissipation to avoid temperatures soaring above the max operating temperature will benefit the system in better performance, longer life and a lower risk of failure.
“electronic component vendors all must test their products to ensure that they perform as expected under specified conditions and to determine their typical performance life,” wrote sandhu.
the article detailed a specific case in which a manufacturer tested surface mount resistors to “ensure the performance, reliability, and typical life expectancy of the components it supplies.”
by viewing the resistors under ti cameras, the engineers were able to observe the thermal patterns in the resistors and its behavior under certain conditions. the addition of a macro lens gave another dimension to the data and allowed the engineers to spot potential issues that they might have otherwise missed.
“with the information gained from the thermal images, the engineer would be able to change the design or the manufacturing process to mitigate the stress points that are creating the hot spot,” said sandhu.
a second case study was given as an example of how ti cameras can assist at the verification stage. spotting a hotspot, the engineers discovered that the power supply was operating above the maximum temperature allowed at 24 volts. when tested at 12 volts, the product dissipated the proper amount of heat. the product was forced to go into redesign before being produced for sale.
sandhu concluded, “with the decrease in component sizes and increased performance demands, heat management of electronics devices and circuits is becoming more significant and important.”
read the full article at http://www.ept.ca/features/use-infrared-thermography-electronics.
|